SinterCell™ Technology
The Scientist And The Engineer
The best way to predict the future is to create it.
Two of the world’s leading authorities on wet fiber molding, Dr. Björn Nilsson and Tony Krey, form the basis for our SinterCellTM technology
SinterCell™
The Art and Science of
Cellulose Engineering
The SinterCell™ 200
Fiber Molding Machine
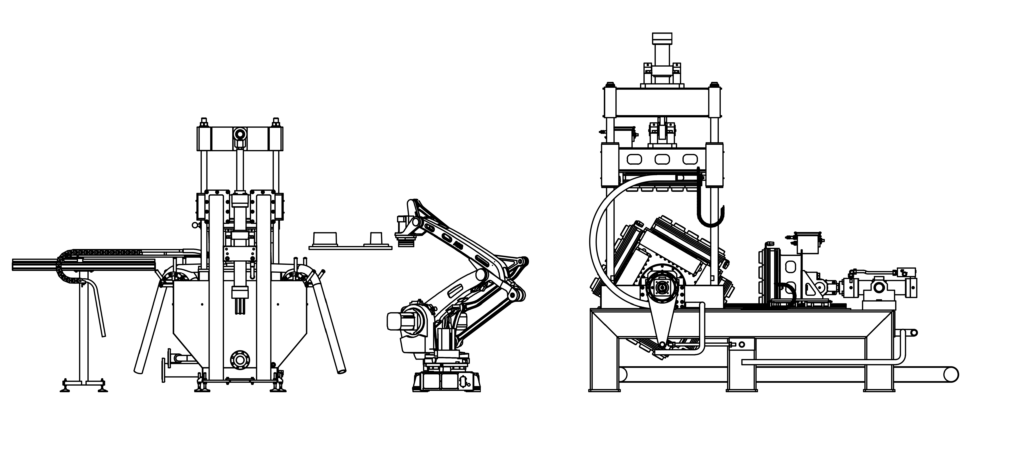
Quality End-Product
The end-products have all the characteristics of plastics but all the environmental benefits of natural cellulose fibers.
Circular Economy Ready
The process renders the cellulose fibers 100% reusable, meaning our products are “circular economy ready” in addition to being fully compostable and recyclable
Engineered for High Productivity
It enables higher productivity and production levels across CAPEX/OPEX investments resulting in industry leading financial returns.